Service & Capabilities
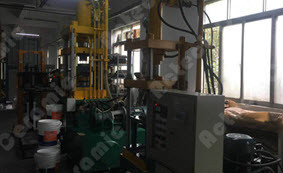
Ceramic Moulding
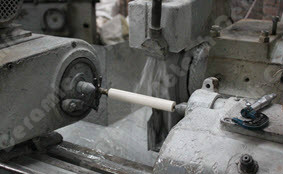
Machining & Grinding
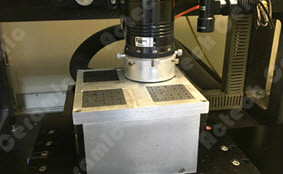
Laser Machining
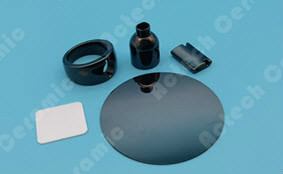
Ceramic Injection Moulding (CIM) is an advanced manufacturing technology. An innovative production process providing cost effective solutions through complex net shape technical ceramic components in medium to large size batches. By being able to produce within or near net shape we can limit or even exclude post-machining, reducing time and labor, thus cost. We help you to maximize benefit of the outstanding properties that technical ceramics offer. With our dedicated knowledge and expertise of material we support you with selecting, designing and processing your advanced ceramic solutions through CIM.
Available material for Ceramic Injection Moulding: 99% Alumina, Zirconia.
Standard Tolerance: ISO2768-m
size limitations: Max. 50mm
Isostatic pressing enables to produce various types of materials from powder compacts by reducing the porosity of powder mixture. The powder mixture is compacted and encapsulated using isostatic pressure, it means by using pressure equally from all directions.
According to the way of creating of the isostatic pressure we recognize hot and cold isostatic pressing. In the case of cold isostatic pressing ,the isostatic pressure is created by applying of the external pressure onto the water or oil and the subsequently onto the encapsulated powder mixture. Apart from moulding with no defect and homogeneous density and complex shapes, it also can achieve the goal of high pressure which will add up to 400 MPa~500MPa.Thus this process ensure to improve the compact of the molding and create favorable condition for subsequent sintering compact.
Dry Pressing is generally used for high volume production and low unit cost. Dry Pressings can be formed in a variety of sizes and shapes. This method requires production tooling which can be expensive, although the high production rates generally amortize this cost to a fraction of the component’s value. With our range of fully automatic presses, used together with high quality tool steel or tungsten carbide tooling, we can ensure high quality and uniformity in our Dry Pressed products.
Dry pressing is ideally suited to the formation of simple solid shapes and consists of three basic steps: filling the die, compacting the contents, and ejecting the pressed solid. Because the dry-pressing process is so simple and involves low capital equipment costs it is the most widely used high-volume forming process for ceramics. Production rates depend on the size and shape of the part and on the type of press used. For large components such as refractories or complex parts such as grinding wheels the production rates are 1–15 parts per minute
Actech offers custom precision ceramic machining and grinding services of tight tolerance components, Owing to the ceramic property of high hardness and wear resistant, its machining method is not so many, by means of which is grinding machining only, but we have diversified machining techniques, we can choose suitable machining technique and equipment in accord with customers’ different products.
Our machining services including:
Lapping is a machining process in which two surfaces are rubbed together with an abrasive between them, by hand movement or using a machine. utilized to control a ceramic or other substrate’s surface finish, thickness, parallelism, and flatness, and the process varies depending upon the type of material and the physical dimensions required.
Lapping can be used to obtain a specific surface roughness; it is also used to obtain very accurate surfaces, usually very flat surfaces.
Polishing is the process of creating a smooth and shiny surface by rubbing it or by applying a chemical treatment, leaving a clean surface with a significant specular reflection. In some materials , polishing is also able to reduce diffuse reflection to minimal values.
When an unpolished surface is magnified thousands of times, it usually looks like a succession of mountains and valleys. By repeated abrasion, those “mountains” are worn down until they are flat or just small “hills.” The process of polishing with abrasives starts with a coarse grain size and gradually proceeds to the finer ones to efficiently flatten the surface imperfections and to obtain optimal results.